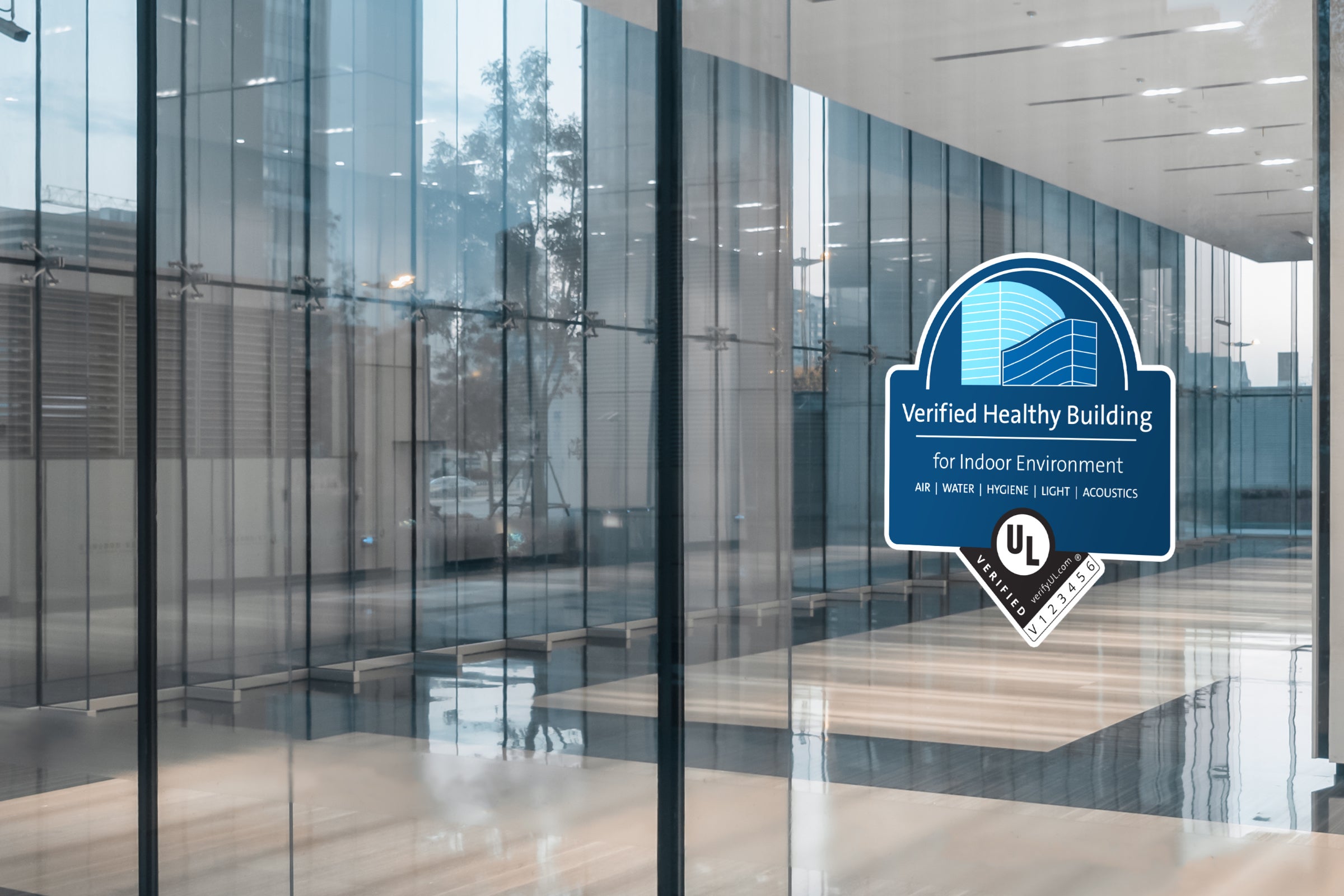
Healthier and more sustainable buildings
Indoor spaces that support human health and wellness have never been more important. In a 2020 survey from “A New Investor Consensus,” published by the Center for Active Design and Fitwel, UNEP FI, and BantallGreenOak, 87% of respondents experienced increased demand for healthy buildings over the past 12 to 24 months, and 92% expect demand to grow over the next three years. Additionally, almost 90% of participants plan to enhance their health and wellness strategy in the next year.
Demand is growing for healthier indoor spaces, and building owners and operators will need to address tenant and occupant concerns by creating indoor environments that support occupant health and well-being.
UL Solutions’ extensive experience in the healthy building space and science-based review process can help you meet these growing demands. Our multidisciplinary team has the expertise and testing capabilities in a range of services, including:
- Evaluation of indoor environmental quality (IEQ) with UL Verified Healthy Building Program
- Ventilation Assessments (ASHRAE Standard 62.1)
- Environmental, social and corporate governance (ESG) and Global Real Estate Sustainability Benchmark (GRESB) Advisory
- Comprehensive green building expertise, including LEED, BREEAM and CHPS
- Integrating health and wellness certifications, including Fitwel and WELL
- Energy and Water Benchmarking services
- Energy Audits — ASHRAE Level I, II and III
- Commissioning (Cx) and Retro and Recommissioning (RCx) services
Our services
Verified Healthy Building Program
The UL Verified Healthy Building Program helps building and business owners communicate their commitment to maintaining healthy buildings and report their efforts to a growing contingent of stakeholders, including investors, tenants, government agencies and consumers.
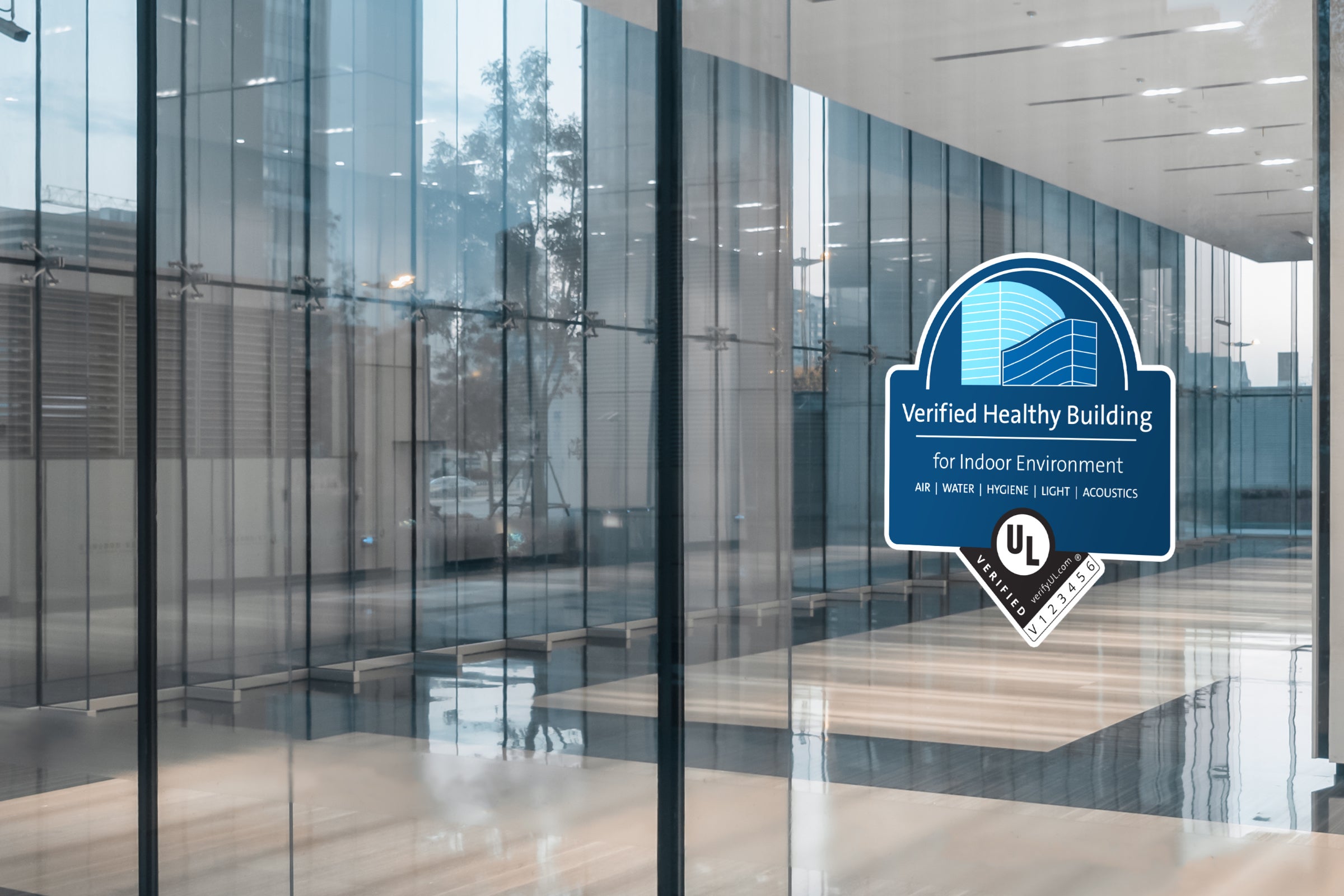
Indoor environmental quality services for Healthy Buildings
Explore the path to healthier indoor spaces with UL Solutions’ expert-led IEQ testing services that help provide confidence to occupants, building owners, stakeholders and the public you’re working to keep them safe.
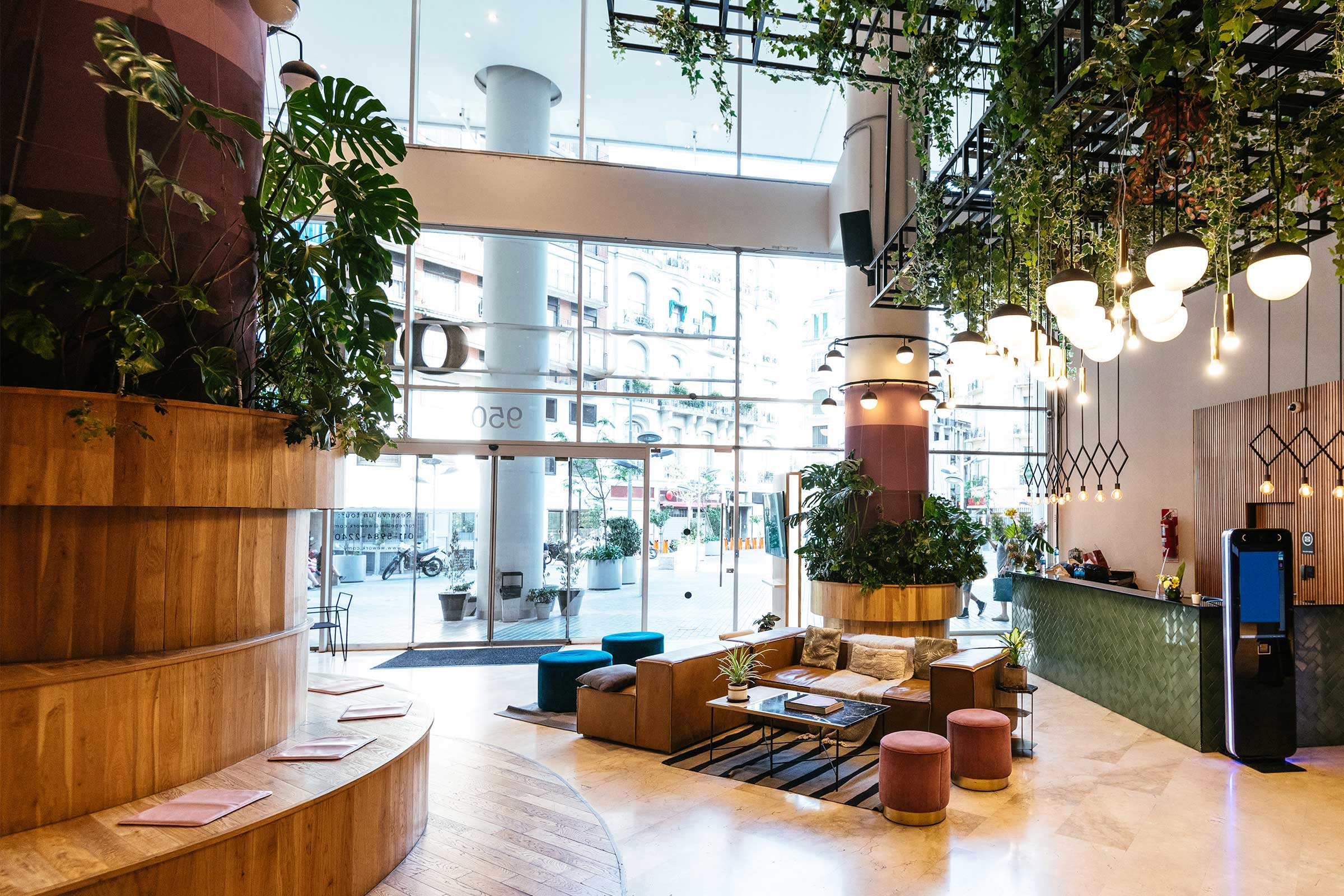
Sustainability services
UL Solutions provides comprehensive support to our customers in their pursuit of building sustainability certifications. We work as an extension of our customers’ internal teams from project inception through certification submission, offering our expertise at every step.
With a proven track record of success, our advisory team employs an integrated approach that focuses on cost-effectiveness, reliability and the triple bottom line (people, profit and planet).
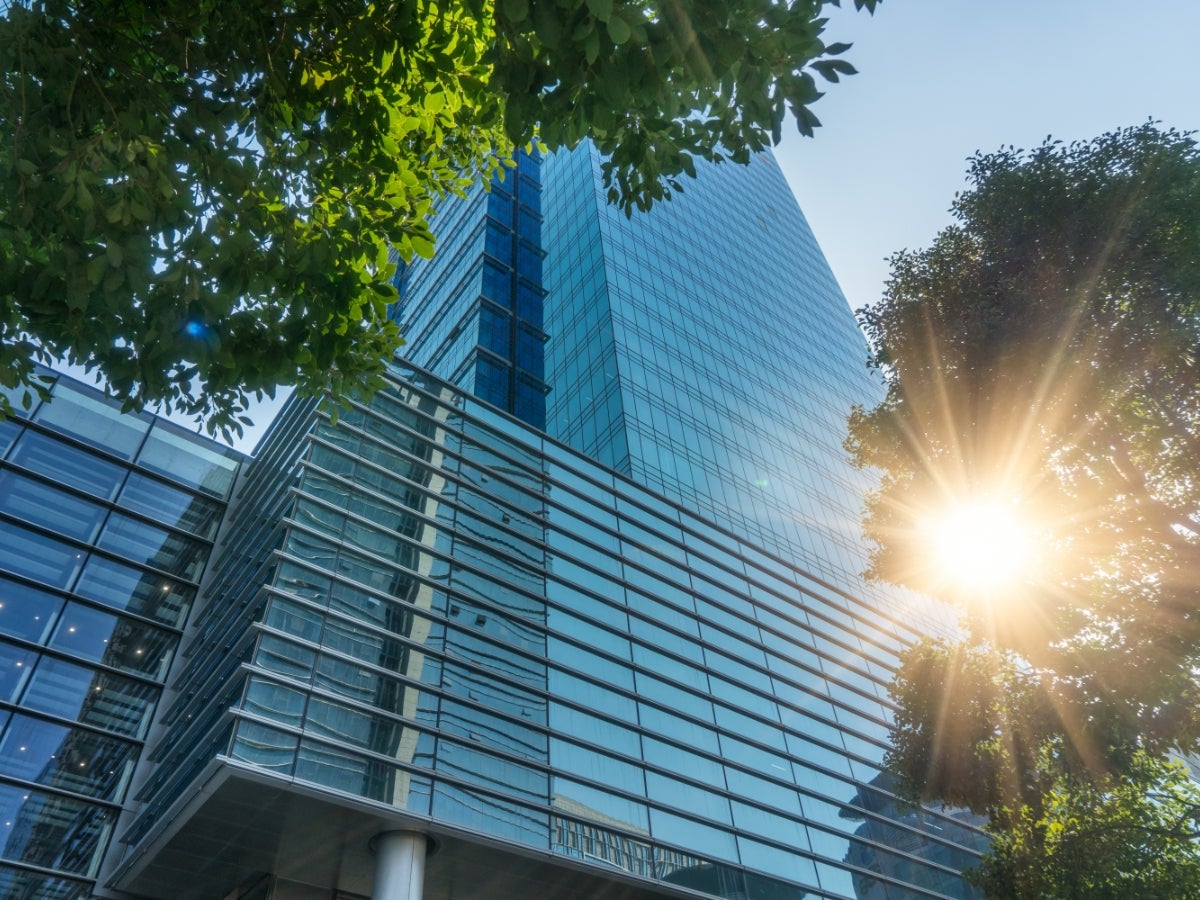
Energy services
As energy requirements and expectations change, you need to understand your buildings’ performance. From energy audits and recommissioning to energy benchmarking, UL Solutions can help.
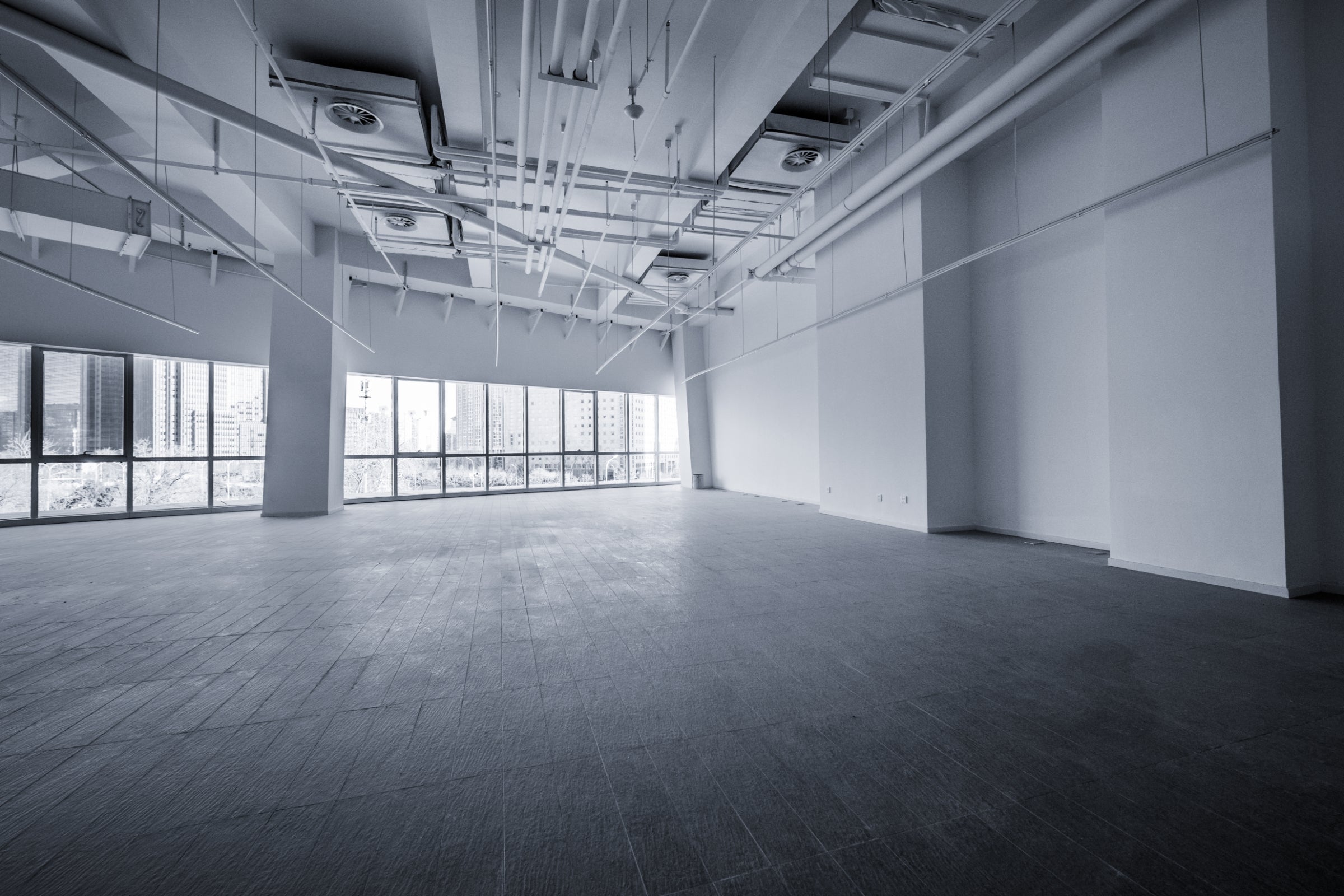
Legionella control
Discover expert-led Legionella control services from UL Solutions that can help you mitigate health and regulatory risk.
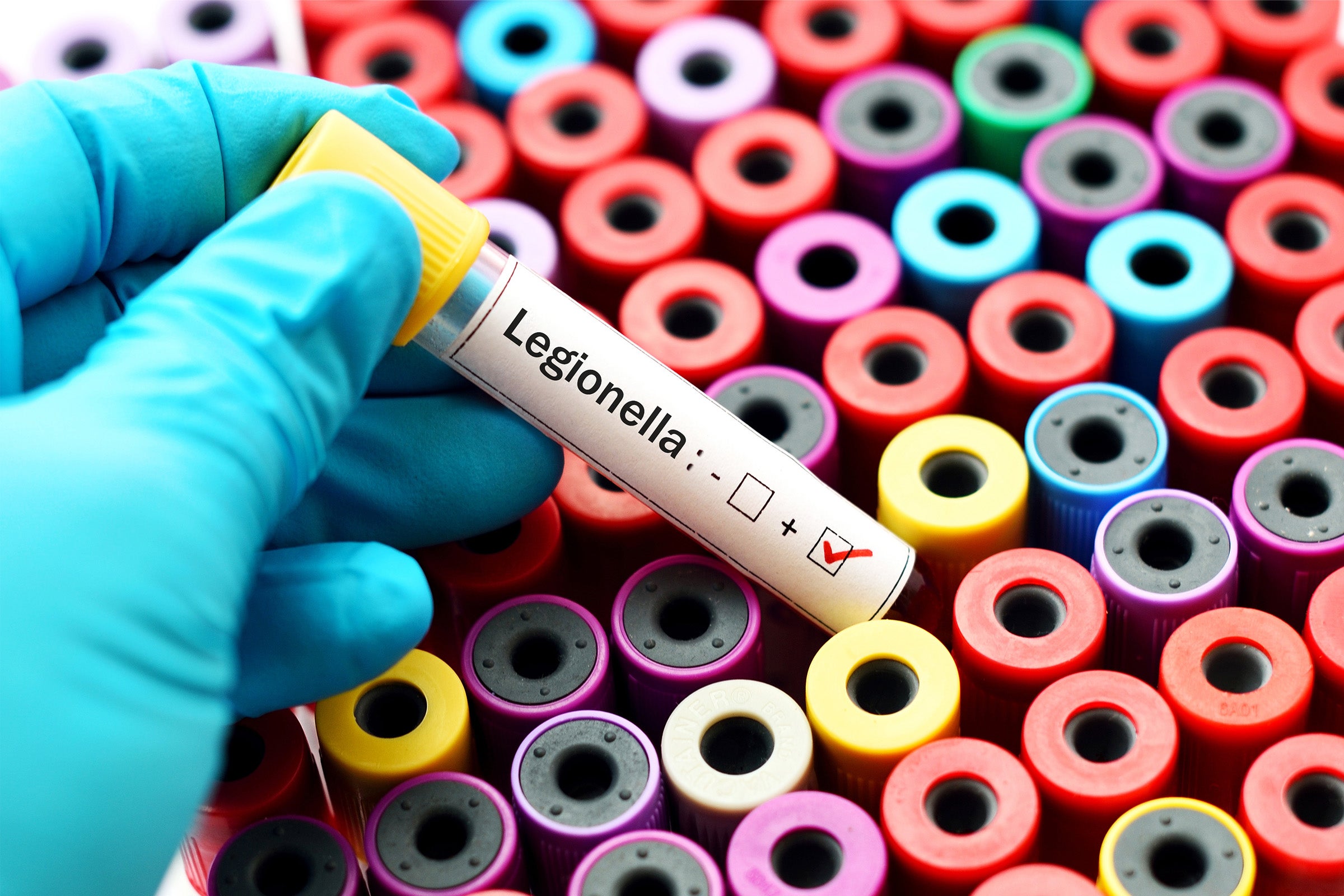
Asbestos management
Find out how UL Solutions can help you manage the ongoing challenge of asbestos in your organization's buildings in the UK and Europe through comprehensive surveys, assessments, training, and removal projects.
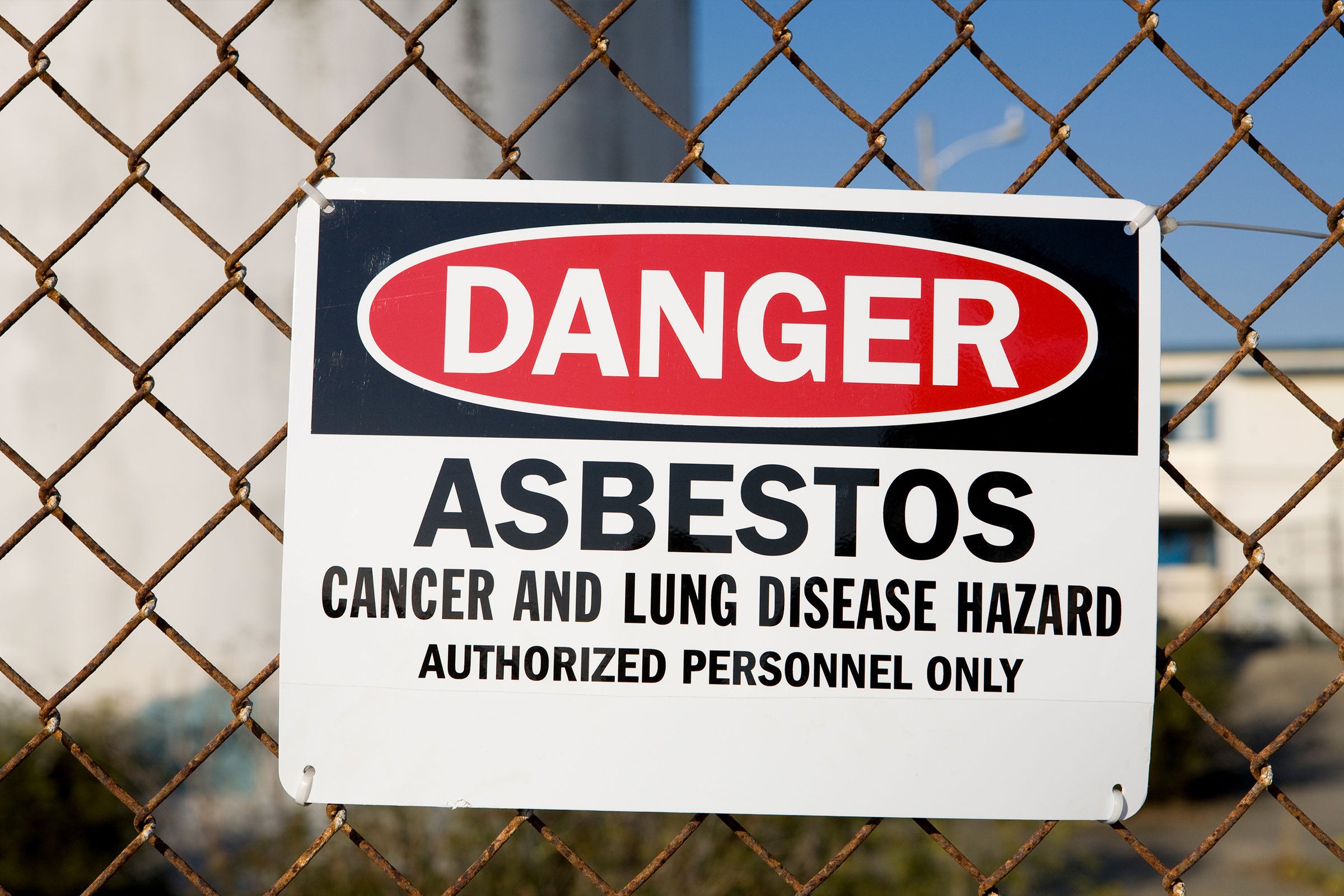
Fire risk assessment
Help protect your UK and European properties from fire risk and comply with regulations through expert-led UL Solutions assessments.
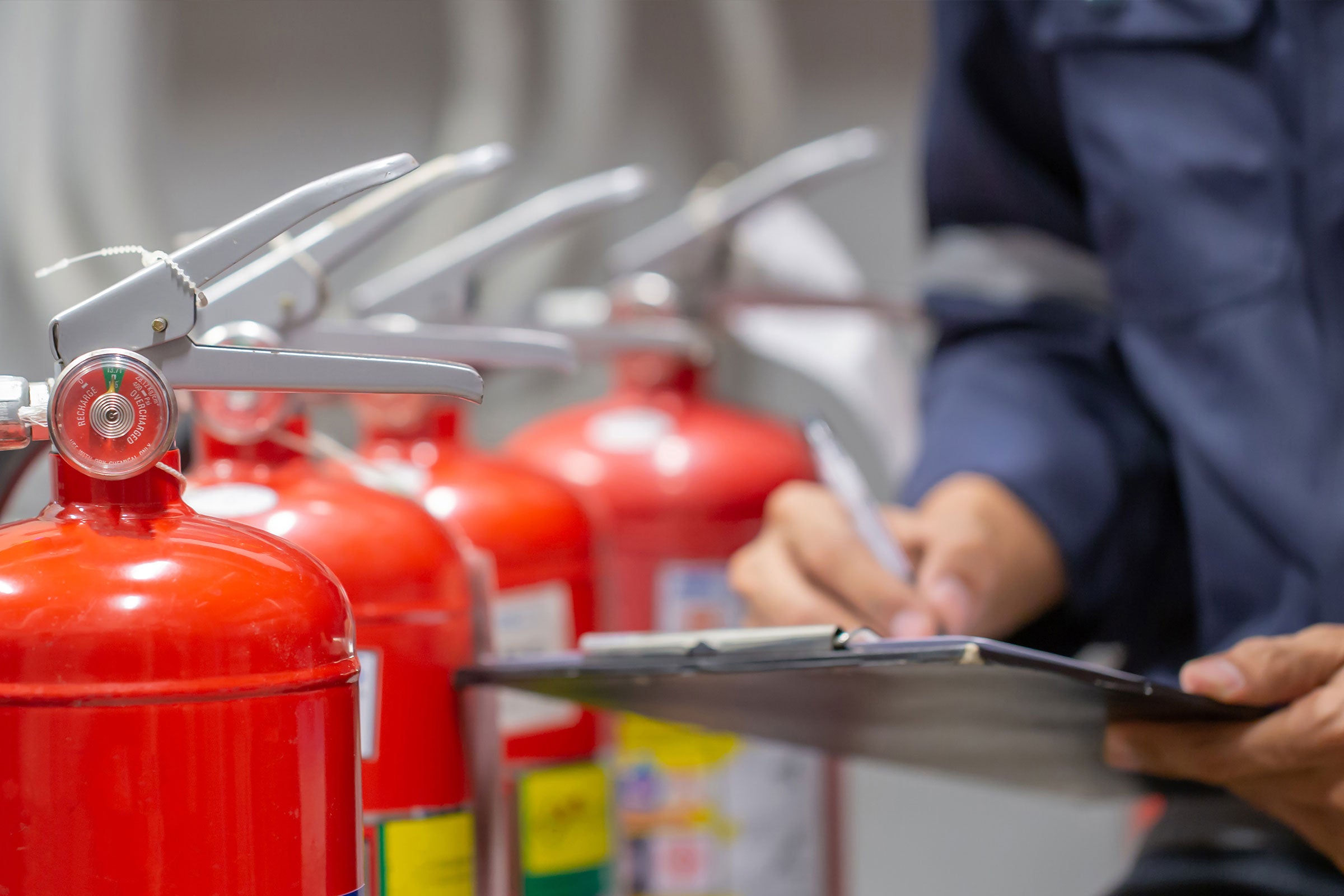
Asbestos and legionella awareness training
Find out how UL Solutions' asbestos and Legionella awareness trainings can educate your team about recognizing and mitigating the risks posed by these harmful substances.
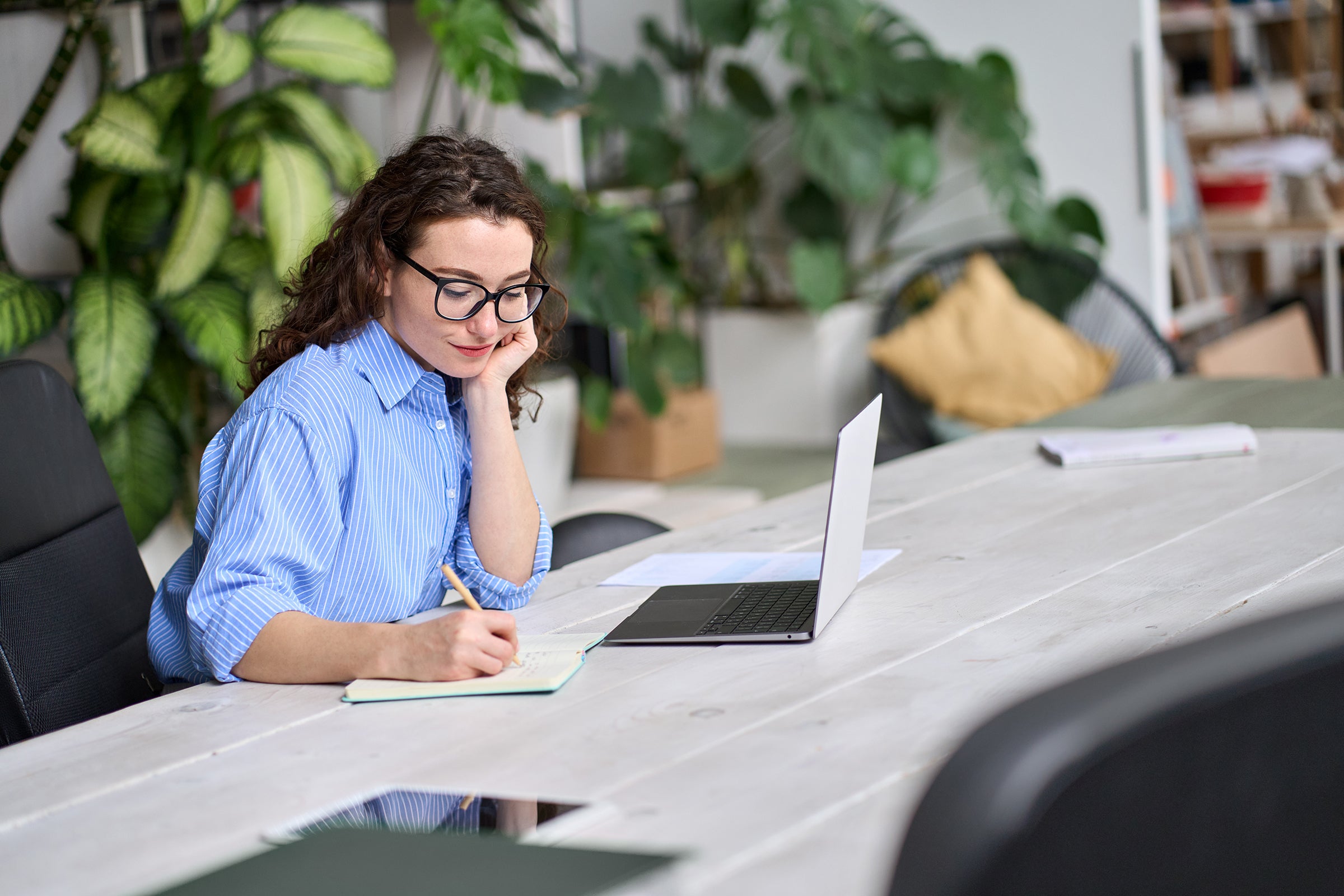
Get in touch
Have questions, need specifics? Let's get this conversation started.