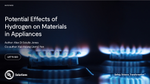
Potential Effects of Hydrogen on Materials in Appliances
A new energy transition targets the reduction of carbon emissions.
Author: Jonathan Brania, PDE manager UL Solutions
In today’s eco-conscious environment, companies are encouraged to reduce greenhouse gas emissions and invest in new technologies to minimize the environmental impact. In the appliances sector, an energy transition has begun with the target of zero CO2 emission and reducing the use of natural gases. The main challenge is to increase safety and efficiency of the appliances while operating with new fuel types, like hydrogen.
As the world takes steps to decarbonize its energy, hydrogen is considered a key contributor to the decarbonization effort, specifically for fuel gas appliances — both as a blend with natural gas, and potentially as a standalone fuel gas. Globally, there are hundreds of projects assessing the feasibility, performance and limits of hydrogen blends — not just for their effects on appliances but whether the current distribution infrastructure can safely deliver blended fuel to consumers.
Many utilities are at the early stages, working to characterize the amount of hydrogen that naturally occurs in their natural gas, while piloting hydrogen blends in the low- to mid-single digits. At the other end of the spectrum are projects like Leeds City Gate in the U.K., which is studying a transition to essentially pure hydrogen as a fuel source.
Based on studies and reports examining the effects on performance for existing natural gas appliances, results showed general favorability for approximately 20% hydrogen blends with natural gas.1
The volume and variety of these projects are motivated by interests as numerous as the utility companies themselves. They are influenced by a host of factors, ranging from government targets and international agreements, to environmental, social, and governance (ESG) interests and corporate social responsibility (CSR), company metrics for carbon reduction, and shareholder activism. This is underpinned by a need for the utilities to provide safe and reliable sources of energy.
Gas-fired appliance manufacturers are simultaneously in the unenviable position of trying to design products capable of performing safely across a spectrum of outcomes, with an acknowledgment that multiple solutions may be needed for different ranges of hydrogen blends. This is all occurring in front of a backdrop of interests that support electrification rather than gaseous fuels as the way forward to reduce carbon emissions.
At the stoichiometric level, the combustion of a methane molecule (CH4) in the presence of oxygen (O2) creates two products: carbon dioxide (CO2) and water vapor (H2O). Stoichiometry is a sort of “perfect world” calculation, allowing chemistry theory to predict the reaction that will occur. In reality, other carbon-based emissions may also manifest, such as carbon monoxide (CO), the creation of which can be influenced by appliance design and environmental conditions. Natural gas is otherwise a cleaner alternative to other carbon-based fuels, such as coal. Still, recent attention on reducing carbon emissions has focused on the creation of carbon dioxide when burning methane, and thus an effort to reduce or eliminate the amount of CO2 created during the combustion process.
CH4 + 2O2 -> CO2 + 2H2O
When burning hydrogen in the presence of oxygen, a similar stoichiometric assessment results in one product: water vapor. As a way to reduce end use carbon emissions, utilities are looking to replace percentages of natural gas with hydrogen and focusing on ensuring that safety and performance levels of new and existing appliances are maintained.
2H2 + O2 -> 2H2O
Numerous studies have been conducted to understand the impacts of blending hydrogen with typical gaseous fuels, including natural gas, which is predominantly methane. As the lightest element on the periodic table, hydrogen is less dense than methane, with a lower calorific (heating) value of about 1/3 compared to a similar volume of methane. The flame temperature for hydrogen is also about 10% hotter when compared to methane. This combination of factors supports the industry consensus that mixtures of about 20% hydrogen or less are compatible with existing burner/appliance designs. However, as the H2 percentage increases, so does the potential for undesirable phenomena and risk.
Compared to typical fuel gases, hydrogen is less dense and has a higher flame speed. For a burner/appliance optimized for performance with a certain type of gas, introducing a gas with a higher flame speed can result in the flame burning closer to the port, which can increase the temperature of the burner itself. More severe circumstances allow the flame to propagate inside the burner. This condition is called lightback or flashback, and leads to incomplete combustion of the gas, significantly diminished performance, and potential damage to the burner and appliance. Lightback can be verified visually, and sometimes audibly with a noticeable rumble as the flame burns inside of the port.
Certain product types incorporate flame supervision devices (FSDs) that interrupt the flow of gas if the burner is inadvertently extinguished. An FSD that senses temperature is not expected to be impacted. However, devices that rely on other principles, such as radiation generated as part of the combustion process, may be impacted.
Hydrogen flames emit little visible light, which is a contrast to the signature blue natural gas flame. The effect is relatively limited for lower percentage hydrogen blends but will be more noticeable for higher concentrations of hydrogen. Where safety is partly managed by the ability to see the flame, such as for a hob or cooktop burner, additional safeguards may be needed at the appliance to promote safe appliance operation when using elevated levels of hydrogen.
For gas-fired appliances, a performance assessment will be needed to examine the effects resulting from the burner’s design. Of particular interest are the flame characteristics, which are related to port sizing, i.e., the burner openings intended to support a flame. Ports are deliberately spaced apart from each other and carefully sized to accommodate gas supplied at a particular pressure. That pressure results in a flow of gas through the burner’s ports that accounts for two velocities: 1) the speed of the gas as it exits the burner through the port; and 2) the speed of the flame that is created from a continuous supply of gas. When designed correctly, a balance results between these two velocities, manifesting in the presence of a stable flame at each port.
It is difficult to recall an era marked by as much disruption as what gas-fired appliance manufacturers face today. Possible gaseous fuels span from no hydrogen to potentially all hydrogen, with various blended percentages in between. The mix of gas-fired appliances and electric appliances may also differ in as little as five years.
Is it possible that some gas utilities will consider another interim step, which could include returning to the era of manufactured gas? Manufactured gas, also known as town gas or coal gas — because it was derived from coal — was widely available over a century ago. It gradually fell out of favor, partly attributable to containing elevated percentages of carbon monoxide. Today, people also focus on where a fuel comes from and how it is created, so it’s not necessarily true that coal gas will make a comeback. But manufactured gas also contained approximately 50% H2, which could provide some historical perspective for how to transport and use something closer to a 50:50 blend of hydrogen and methane.
As manufacturers and their suppliers seek to develop solutions, research and test laboratories can be an important contributor and validator, simulating and blending gases to determine how burners/appliances will operate over a range of current and future fuel gases. This testing can then be used to inform regulators and safety standard technical committees where changes are needed in installation codes and gas-fired appliance standards.
While some combustion engineers rely on reference materials from many decades ago, there may be tools even deeper in our past that hold some of the keys to our future. Not every innovation will be as simple as the old becoming new, but it is clear that the hydrogen fuel era will mark another cycle of change for the appliance industry.
Partnering with UL Solutions — a global safety science leader for advisory, benchmarking, and certification services — can help build customer confidence and trust in products that manufacturers are launching on the market.
References
Potential Effects of Hydrogen on Materials in Appliances
Thanks for your interest in our products and services. Let's collect some information so we can connect you with the right person.