
As the energy transition drives electrification in the automotive and other transportation industries and the surging demand for battery energy storage systems (BESS), UL Solutions has opened the doors of its North America Advanced Battery Laboratory in the Auburn Hills Oakland Technology Park complex, near one of the world’s largest automotive hubs — Detroit, Mich.
At this facility, UL Solutions experts use cutting-edge battery testing equipment and methodologies to deliver comprehensive safety testing and performance services for the EV and Industrial batteries markets — all under one roof.
Testing services for electric vehicles (EVs)
UL Solutions offers comprehensive automotive battery testing services at the cell, module and pack levels to validate performance, reliability, safety and other key characteristics that help differentiate your products.
We stand committed to supporting the electrification of the automotive and other transportation industries by testing and certifying electric vehicle (EV) batteries for compliance with standards, regulatory requirements and original manufacturer (OEM) specifications. We can also create customized testing service packages to meet our customers’ specific needs.

Passenger vehicles

Commercial vehicles (Class 1-8)

Industrial vehicles

Buses

E-motorcycles

Construction, agriculture and mining vehicles

Watercraft

Aircraft

Airport ground support equipment (GSE)

Recreational vehicles, including snowmobiles, golf carts and all-terrain vehicles (ATVs)
Performance and abuse testing
Performance testing
- High-temperature operating endurance (HTOE)
- Low-temperature operating endurance (LTOE)
- Powered thermal cycling endurance (PTCE)
- High temperature high humidity endurance (HTHE)
- Functional performance verification
- Thermal mapping
- Durability testing/cycle life
- Dynamic stress testing
- Storage loss/calendar life
- Self-discharge
Mechanical testing
- One K350 vibration table (350 kN force)
- Two K200 vibration tables (200 kN force)
- Ability to accommodate battery packs up to 3,000 kg
- Mechanical shock testing up to 100 g acceleration
- Vibration testing, including the option for electrical and temperature cycling/control
Abuse testing
- Thermal runaway or thermal runaway propagation testing on battery cells, modules, packs and units
- External fire exposure testing on battery modules and packs (e.g., UN ECE R100 or UL 2580, the Standard for Batteries for Use In Electric Vehicles)
- Electrical safety testing: overcharge, overcurrent, overdischarge, short circuit, etc.
- Cell crush and nail penetration testing
- 0.1 to 80 mm/s crush speed
- Up to 5 kN maximum force
- Adjustable platen and indenter
- Maximum specimen dimensions of 300 x 300 x 200 mm
- Module and pack nail penetration testing
- 0.1 to 80 mm/s crush speed
- Up to 5 kN maximum force
- Flexible design to accommodate various-sized battery packs/modules
- Module and pack crush testing
- 0.1 to 10 mm/s crush speed
- Up to 300 kN maximum force
- Adjustable platen and reaction face
- Capable of accommodating batteries between 185 and 3,100 mm in length
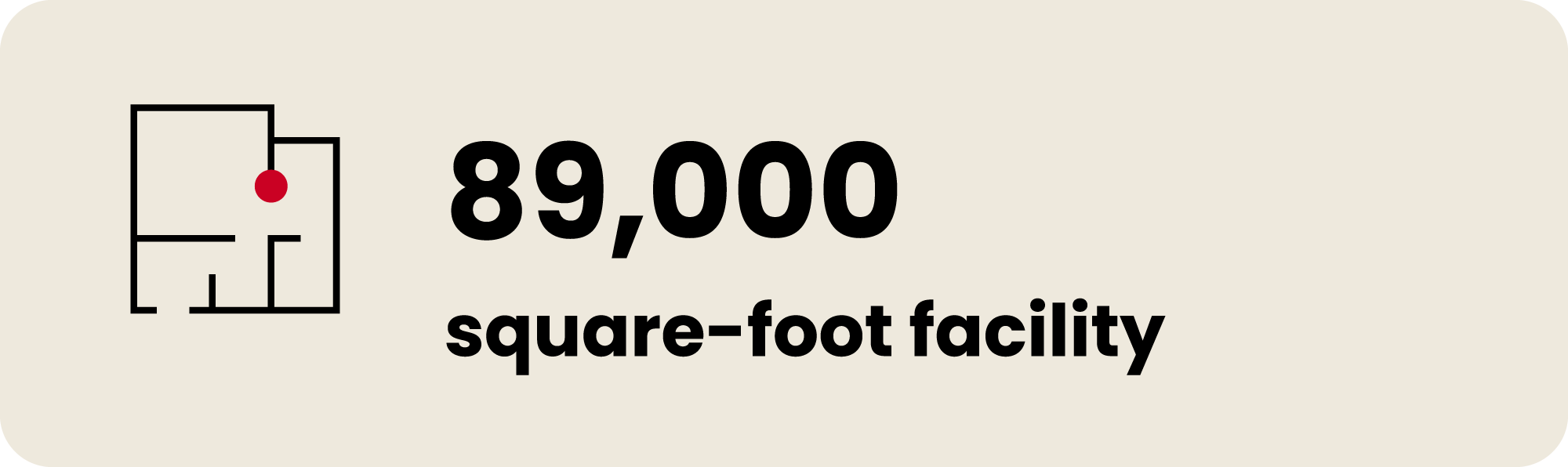
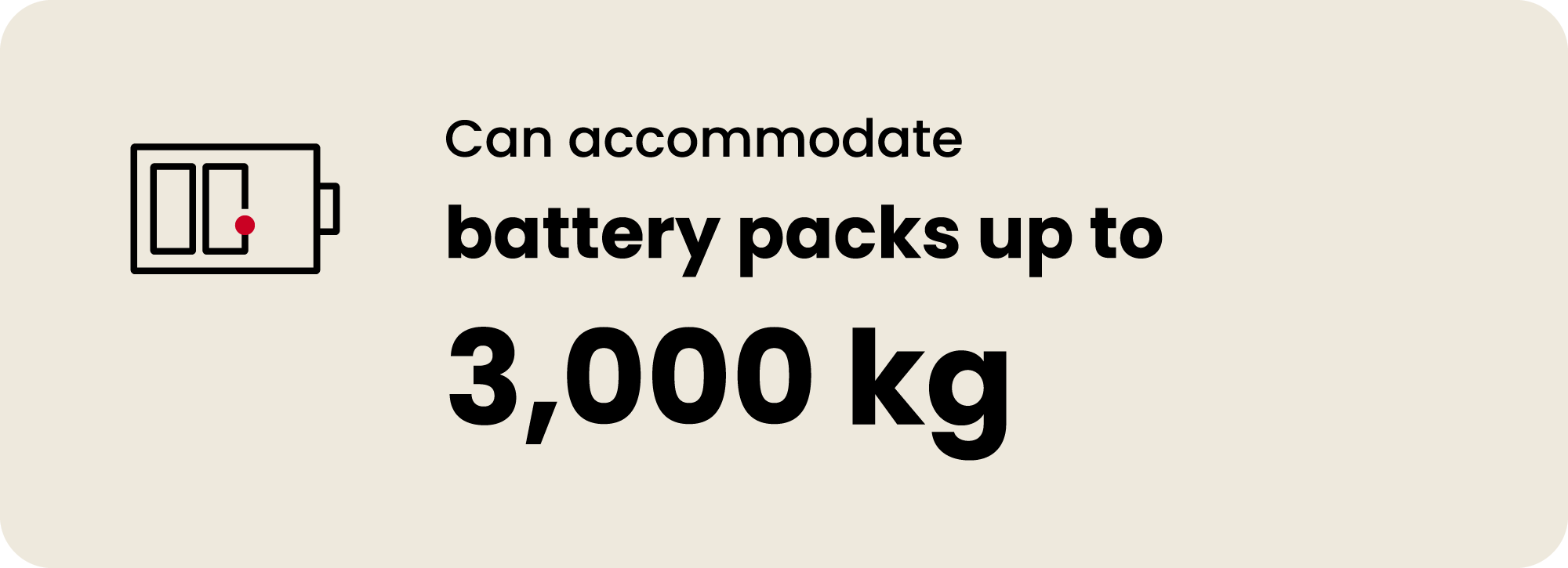
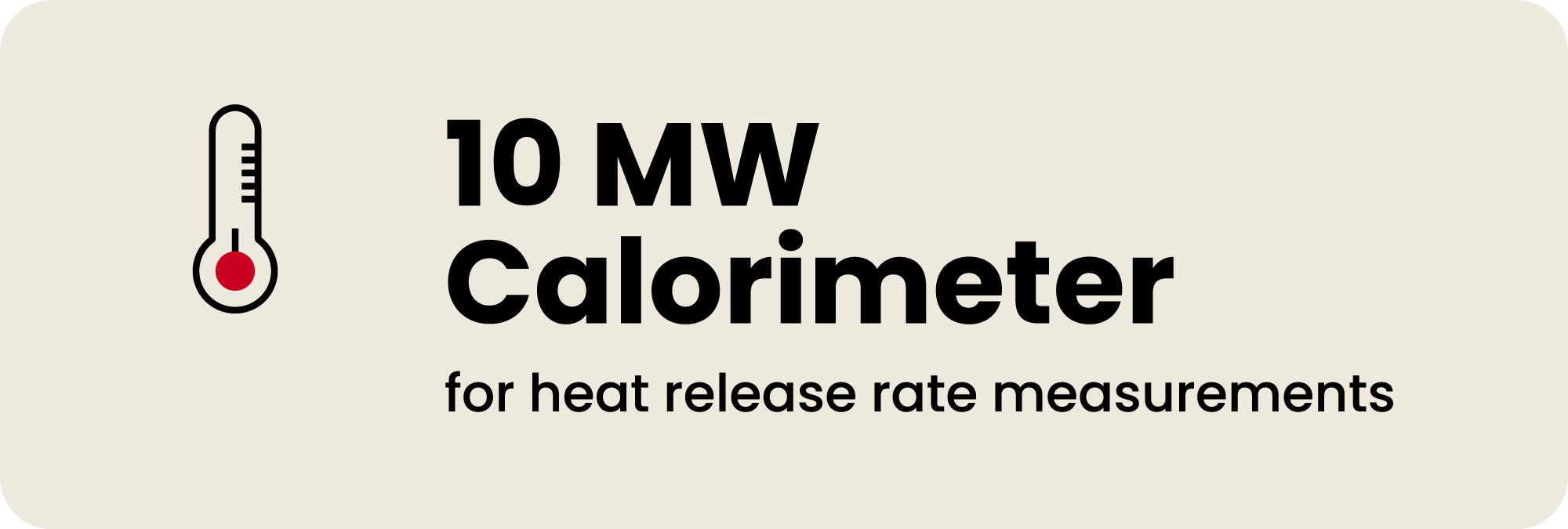
Related resources
Cutting-edge equipment, technology and methodologies
At our 89,000-square-foot facility, our team of specialized engineers and technicians use state-of-the-art equipment, technology and methodologies to deliver robust battery testing services.
Download the brochure with the list of our industry-leading equipment.
Testing for industrial batteries
UL Solutions can test and certify lead-acid, lithium and other forms of electrical, electrochemical, thermal and mechanical energy used in industrial stationary batteries, uninterrupted power supply (UPS) and energy storage devices.
We test to standards and requirements for batteries and energy storage products destined for North American, European and Asian markets, including the following:
- UL 991, the Standard for Tests for Safety-Related Controls Employing Solid-State Devices
- UL 1973, the Standard for Batteries for Use in Stationary and Motive Auxiliary Power Applications
- UL 1998, the Standard for Software in Programmable Components
- UL 9540, the Standard for Energy Storage Systems and Equipment
- UL 9540A, the Standard for Test Method for Evaluating Thermal Runaway Fire Propagation in Battery Energy Storage Systems
- UN 38.3, United Nations (UN) Manual of Tests and Criteria, Lithium Metal, Lithium Ion and Sodium Ion Batteries
- UL 2743, the Standard for Portable Power Packs
- UL 1989, the Standard for Standby Batteries
- IEC 62619, Safety of Lithium Batteries
- IEC 63056, Secondary Cells and Batteries Containing Alkaline or Other Non-acid Electrolytes — Safety Requirements for Secondary Lithium Cells and Batteries, for Use in Industrial Applications
Automotive and EV battery regulatory standards and requirements
- UL 2580, the Standard for Batteries for Use in Electric Vehicles
- SAE J2929, Safety Standard for Electric and Hybrid Vehicle Propulsion Battery Systems Utilizing Lithium-based Rechargeable Cells
- SAE J1798, Performance Rating of Electric Vehicle Battery Modules
- SAE J2380, Vibration Testing of Electric Vehicle Batteries
- UNECE R100 and R136, Uniform provision concerning the approval of vehicles about specific requirements for the electric powertrain
- FMVSS, Federal Motor Vehicle Safety Standards
- CMVSS, Canadian Motor Vehicle Safety Standards
- KMVCC, Korean Motor Vehicle Safety Standards
- LV 124, German automotive manufacturer testing standards
- GB 38031, Safety Requirements for EV Cells and Systems for On-road Applications
- VW 80000, Volkswagen
- GMW 16390, GMW 3172, General Motors Worldwide
- CS.00056, Stellantis
- SDS, TSC3000G, Ford
- ISO 6469-1, Electrically Propelled Road Vehicles – Safety Specifications – Part 1: Rechargeable Energy Storage System (RESS)
- IEC 62660-3, Secondary Lithium-ion Cells for the Propulsion of Electric Road Vehicles – Part 3: Safety Requirements
- IEC 63057, Secondary Cells and Batteries Containing Alkaline or Other Non-acid Electrolytes – Safety Requirements for Secondary Lithium Batteries for Use in Road Vehicles Not for the Propulsion
Connect with our team of battery experts
Thanks for your interest in UL's products and services. Let's collect some information so we can connect you with the right person.