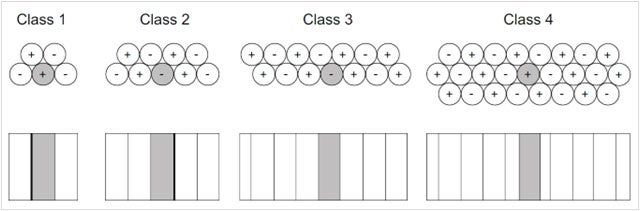
Improving battery safety in flight: UL 5800 fire containment testing
Lithium-ion batteries have become the default power source for most electronic devices, like smart phones and laptops. These rechargeable batteries have been an advantage for device manufacturers and consumers, as they have a high energy potential and maintain their ability to recharge quickly while minimizing the size of the battery. However, their widespread use has also introduced significant safety challenges.
Understanding the role of UL 5800
Lithium-ion batteries and safety concerns
If damaged or incorrectly charged, lithium-ion batteries can experience chemical reactions within their components, including flammable electrolytes, which may lead to a thermal runaway event. This process can escalate into a fire or explosion, posing severe risks in confined environments like aircraft.
The increase in thermal runaway cases
From 2019 to 2023, there was a 28% increase in battery thermal runaway incidents on aircraft, according to a UL Standards & Engagement report from September 2024.
In this article, Kevin Hyland, principal engineer at UL Solutions, explains the test methods within ANSI/CAN/UL 5800, the Standard for Safety for Battery Fire Containment Products.
The development of the UL 5800 Standard
Industry collaboration for enhanced safety
If an incident does occur, airline personnel can use Battery Fire Containment Products to mitigate fires and damage from thermal runaway events during the flight. A growing industry concern was knowing which fire containment products are effective and will meet their respective performance claims.
To combat this, UL Standards & Engagement developed a new safety Standard, Battery Fire Containment Products that would be used to contain lithium-ion battery fires and minimize the related effects during flight. They formed a technical committee of individuals and organizations with interest or technical expertise in the subject category. Participants included international representatives from airlines, shipping companies and other aviation-related organizations, along with government bodies and containment product developers.
Key aspects of the UL 5800 fire containment test
The core test within UL 5800 is a fire performance test, which evaluates the ability of the containment product to mitigate and contain the hazards of a lithium-ion battery thermal runaway. The following summarizes the containment test and its requirements. Consult ANSI/CAN/UL 5800, the Standard for Safety for Battery Fire Containment Products, for complete requirements.
The UL 5800 testing process
Preparing fuel loads and packages
In preparation for the test, a fuel load or package that is representative of the containment product’s intended containment capacity is prepared. The package consists of an acrylonitrile butadiene styrene (ABS) plastic enclosure that is filled with a prescribed quantity of 18650-format lithium-ion cells, as shown in Table 1 and Figure 1 below:
Table 1
Fuel load/package details
Class rating |
Representative capacity in watt-hours (Wh) |
Quantity of 18650-format lithium-ion cells |
Cell configuration |
1 |
0 ≤ 60 |
5 |
2 rows |
2 |
61 ≤ 100 |
9 |
2 rows |
3 |
101 ≤ 160 |
14 |
2 rows |
4 |
161 ≤ 300 |
25 |
3 rows |
Figure 1
Cell stacking and fuel load/package configuration
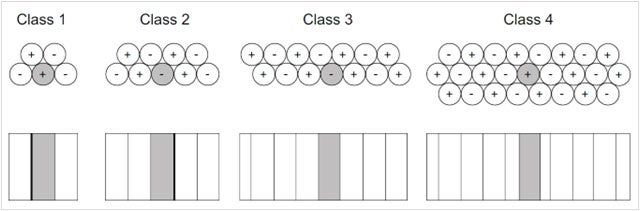
Inside the plastic enclosure, the cells are held in direct thermal contact with each other to enable cell-to-cell thermal runaway propagation. A flexible film heater is wrapped around one centrally located cell, shown in Figure 1.
Next, temperature sensors are placed on the exterior surfaces of the containment product at a density of not less than one sensor per 36 in2 of surface area. At least one sensor is placed on both the product’s exterior surface directly above and below where the fuel load will be placed. Additional sensors can also be placed in other locations, such as dedicated vents, openings, handles, latches or other nonuniform areas.
The fuel load is then placed inside the containment product and secured according to the manufacturer’s instructions.
Creating the testing environment
In the testing laboratory, the containment product is placed on a softwood surface that is covered with white tissue paper and is loosely draped with a single layer of cheesecloth. It is then placed under a collection hood with an exhaust duct, to collect all products of combustion, like smoke and gases. Light transmission measurements in the exhaust duct and the duct flow rate are then used to calculate the total smoke release from the containment product during testing. During this process, a data acquisition system collects temperature and smoke measurements, at a rate of once per second.
The containment test is started by heating the flexible film heater at a rate of 4°C to 7°C per minute until thermal runaway is initiated in the fuel load. Visual observations and data collection are then carried out for six hours to monitor the conditions of acceptance, which can be found in table 2. The test may be stopped sooner than six hours if all cells in the fuel load have undergone thermal runaway and cell temperature has returned to 40°C (104°F).
Table 2
Conditions of acceptance of UL 5800 battery fire containment products – Performance Level 1 and Performance Level 2
Conditions of acceptance |
Performance Level 1 |
Performance Level 2 |
Flames do not breach the containment product as determined by glowing or igniting of the cheesecloth or tissue paper. |
X |
X |
Shrapnel, sparks or other harmful debris of the test do not escape the containment product. |
X |
X |
Surface temperatures of the containment product at any location do not exceed certain values.* |
X |
X |
All visible smoke is confined within the containment product. |
X |
|
No more than 5 m2 of total smoke is released from the containment product. |
|
X |
*See Table 8.2 in ANSI/CAN/UL 5800, the Standard for Safety for Battery Fire Containment Products for the maximum allowed surface temperatures.
Products undergo three consecutive tests, and failure to meet the conditions of acceptance in any test disqualifies the product from certification.
Marking, instruction and packaging
As part of UL 5800, there are also marking, instruction and packaging requirements.
- A containment product with a dedicated vent must be marked with "CAUTION" and "Risk of burn. Avoid contact.”
- Operating instructions, in the form of numerically sequenced pictographs, must illustrate how to use the containment product. The instructions must be externally visible.
- Gloves that comply with either the structural firefighting glove requirements of NFPA 1971 or the Type B welding glove requirements of EN 12477 must be packaged with the containment product.
Ratings and certifications
The containment product must be marked with the class rating (Class 1, Class 2, Class 3 or Class 4) and the performance level (Performance Level 1 or Performance Level 2) following the results of the containment test.
For example, a containment product marked as “Class 2, Performance Level 2” indicates the following:
- It was evaluated for use with portable electronic devices with a maximum electrical energy of 100 Wh.
- During the test, it did not release more than 5 m2 of smoke and contained flames and shrapnel.
- During the test, it kept surface temperatures below the specified threshold.
Containment products certified by UL Solutions to ANSI/CAN/UL 5800 can be found in the online certification directory, UL Product iQ®. Product iQ is available to use at no cost but requires a one-time registration. Search for the product category “Battery Fire Containment Products” (XHCA, XHCA7), or view the list of current certifications and the Guide Information page.
Benefits of aligning with UL 5800
Improved fire management for airlines
By aligning with UL 5800, airlines gain access to fire containment products that provide robust safety measures against lithium-ion battery incidents. This helps protect passengers and crew while maintaining compliance with evolving aviation safety standards.
Supporting battery manufacturers with safety standards
UL 5800 offers battery manufacturers a framework to design products that meet stringent safety criteria, reducing the risks associated with lithium-ion battery thermal runaway. This alignment enhances marketability and consumer trust.
The importance of adopting evolving safety standards
As the use of lithium-ion batteries continues to grow, so do the associated safety challenges. Standards like UL 5800 play a critical role in safeguarding aviation and other industries by providing comprehensive guidelines for fire containment products. Adopting evolving standards is essential to enhancing safety, aligning with regulatory expectations and advancing fire containment technology.
FAQs
- Can a battery fire containment product certified to UL 5800 be used in the inhabited compartment of a sea-going vessel or an industrial setting?
Battery fire containment products certified to UL 5800 are intended to be used by a qualified or trained person for portable electronic devices (PEDs) in inhabited aircraft compartments. The conditions of acceptance in UL 5800 are based on this intended use.
If used in other locations or situations, a containment product certified to UL 5800 would be expected to perform in the same manner as in the inhabited aircraft compartment. However, depending on the code authority, some of the conditions of acceptance may be of less concern.
The fire condition represented by UL 5800 is currently limited to PEDs with electrical energy with a maximum of 300 Wh. In industrial settings, the size of devices and quantity of electrical energy could be significantly greater and require larger containment products that would not fit in an inhabited aircraft compartment.
- Why is the quantity of smoke expressed with an area unit and not with a volume unit?
To clarify the units of this measurement, light obscuration is measured as a unitless ratio of light transmission between a clear beam and signal during test. Volumetric flow rate in the duct is normalized by the path length of the beam, resulting in units of m2 instead of the volumetric unit of m3. This is not suggesting that the smoke is considered two-dimensional, but that the measurement is independent of the duct diameter.
- Does the Federal Aviation Administration (FAA) or other global aviation regulatory authorities require or give credit for UL 5800 compliance of containment products?
While the FAA currently does not require compliance to UL 5800, the FAA Advisory Circular 120-80B, Firefighting of General and High-Energy In-Flight Fires (dated March 16, 2023) states, “[ANSI/CAN/UL 5800, the Standard for Safety for Battery Fire Containment Products] includes testing and certification and should reduce the risk of in-flight TR [thermal runaway] events in the future.”
Get connected with our sales team
Thanks for your interest in our products and services. Let's collect some information so we can connect you with the right person.