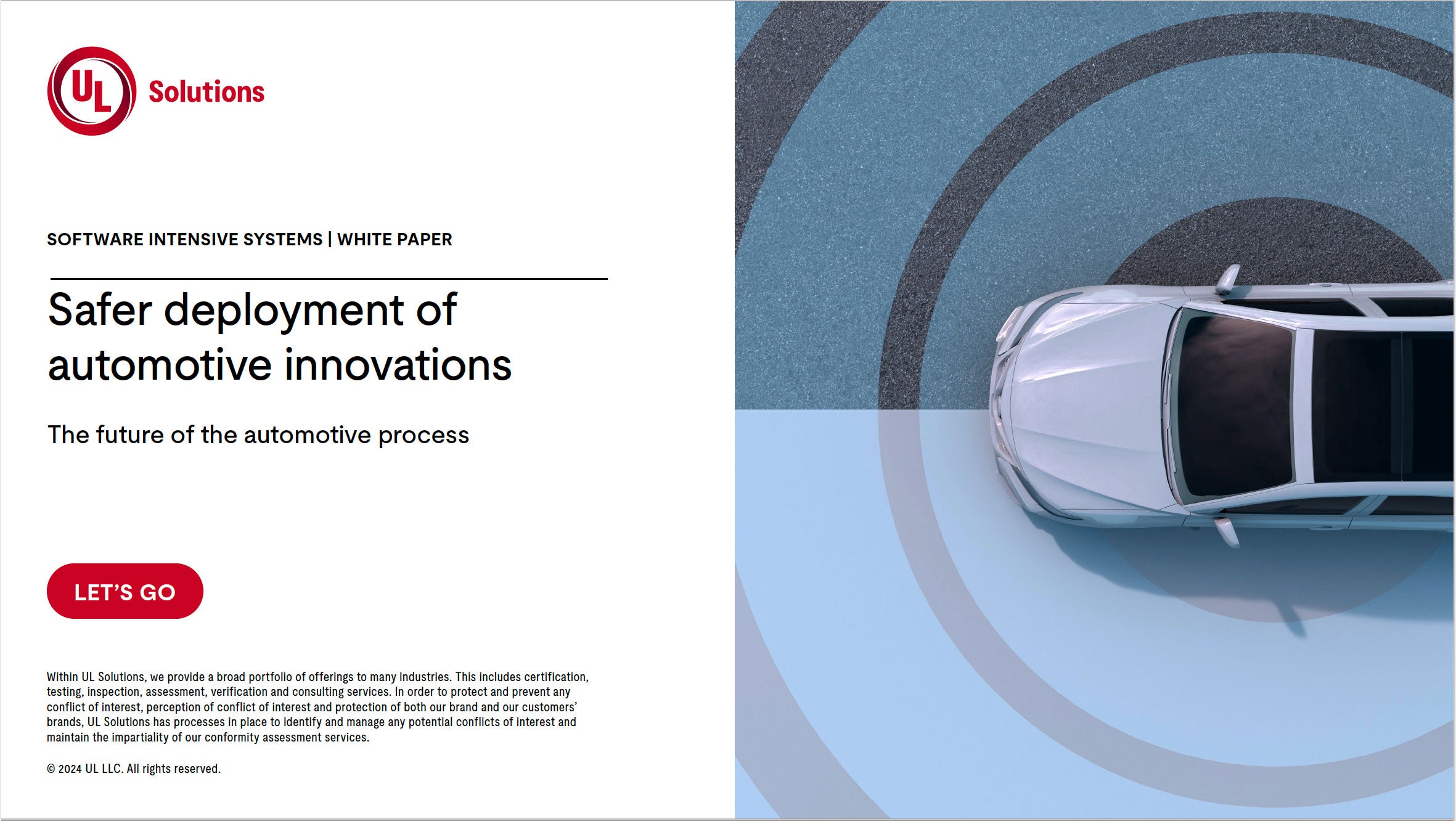
How does your company keep pace with advancing technology while increasing consumer confidence in the safety and security of its automotive products?
Embedded and systems software is a significant driver of automotive technological innovation. In order to keep pace with the speed of new technology, existing and emerging industry standards need to address risks at a similar rate. These standards include ISO 26262 for functional safety, ISO 21448:2022 for safety of the intended function (SOTIF), and ISO/SAE 21434 for vehicle cybersecurity. Moreover, new players need to understand how to get the most out of established standards like IATF 16949 (based on APQP) and how Automotive SPICE® helps improve the quality of complex software and systems.
Future automotive challenges are interconnected and have a common denominator: the processes used to manage the products across their lifecycles. Consumers need to be able to trust existing processes for safety and security, even as those processes need to become more agile to meet the current speed of innovation.
A Bill of Process (BOP) often captures manufacturing maturity that assures predictable quality. The same mindset applies to decision-making and managing risk when developing and introducing new technology into the marketplace. Stages, our process management tool, helps a product execution proceed based on a proven process that has evolved over time. Lean principles might drive the evolution and are likely caused by quality insights. It can even be driven by a disciplined scientific discovery process when advancing new technologies, e.g., batteries and power electronics in automobile applications.
Consumers and governments want innovation and safer products. The key lies in the fact that they are interconnected and have a common denominator: the product development process (PDP). The processes used to manage development progression need to consider regulatory elements in the context of the base product development rather than an end-of-line quality check. Certification often requires evidence that a product met measurement standards and that the manufacturer performed due diligence to increase product safety.
Engineering experts often develop standards in areas where systemic failures occur. A good standard provides a measurement technique to help decide what conforms and what doesn’t. Such measures improve quality by narrowing variation. With variation in mind, many manufacturers have started thinking of statistical process control (SPC), which is required in standards like IATF-16949 for automotive quality management systems. Some regulations refer to industry standards that must be met to demonstrate that the product was engineered and produced with safety in mind.
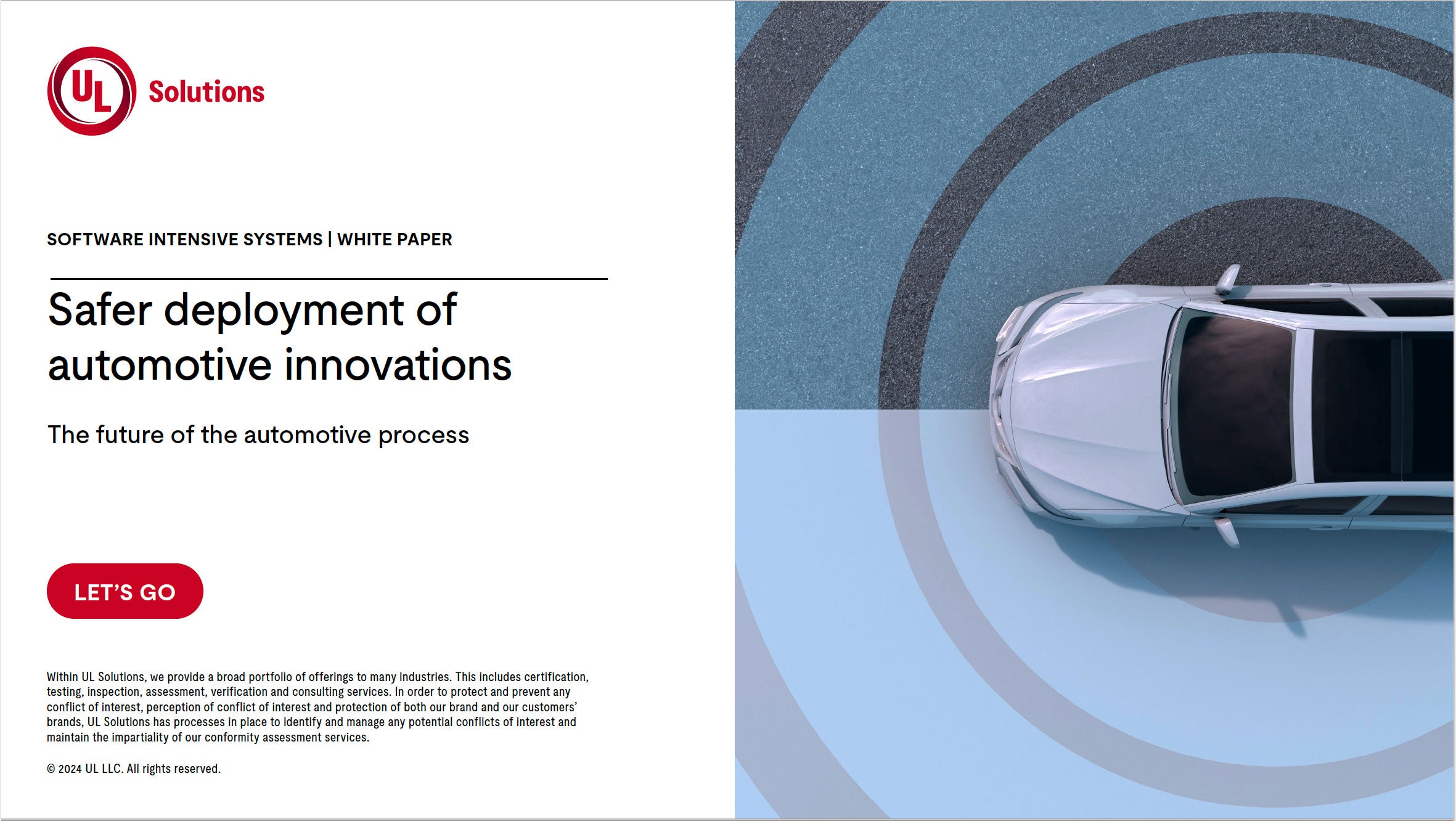
Download our comprehensive white paper and gain additional insight into Stages and product development processes.
Safer deployment of automotive innovations