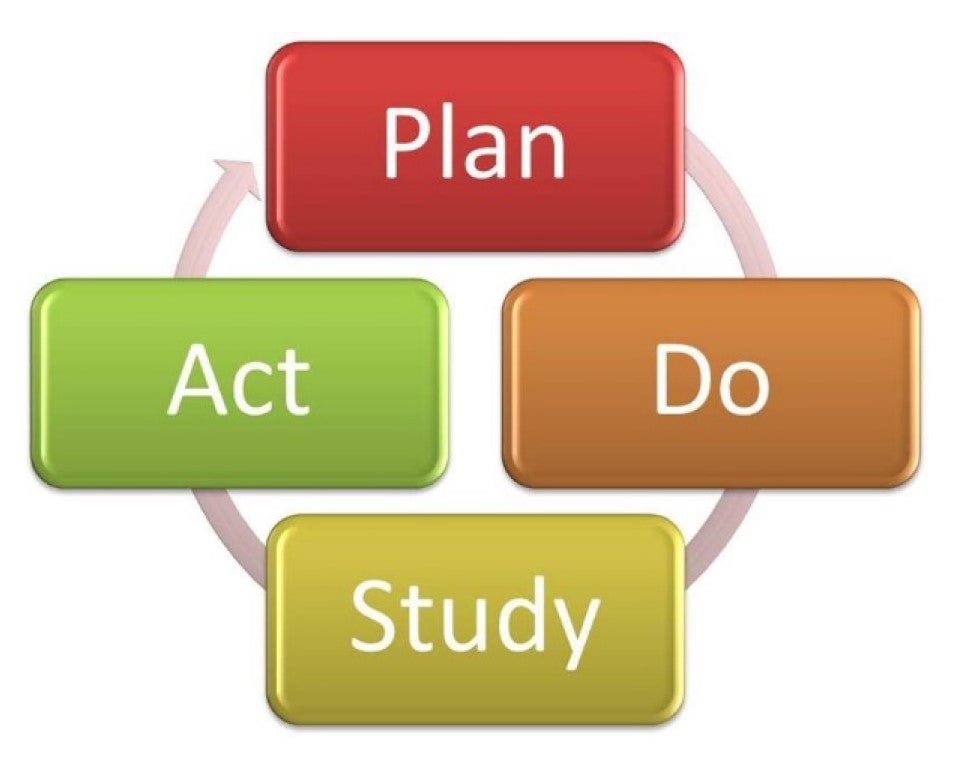
This article examines the many complexities of wire and cable manufacturing and the digital solutions to reduce this complexity.
Countless product iterations, changing customer and market demands, and adherence to specified parameters create many opportunities for error.
This article examines:
- Combating issues created by the complex nature of wire and cable manufacturing.
- Setting and using design standards.
- Managing quality and cost.
- Continuous improvement and problem-solving.
- KPIs and management reviews.
- Modern management and digital solutions.
- Digital solutions for wire and cable manufacturers.
Introduction
Cable types, materials, standards — it’s complex
Wire and cable factories are complex manufacturing environments. A factory’s processes and machines typically produce many different products, even if it specializes in one particular family of cables.
Often, factories manufacture cables from more than one family, using various material combinations. To name but a few, these can include:
- Low, medium or high-voltage cables
- Stranded, flexible or solid conductors
- Copper, aluminum, both or more exotic materials
- Telecommunications, including optical, data or energy cables
- Rubber, PVC, polyethylene, paper
- Buried, surface or sub-sea cables
Cables may also be produced to various national and international standards, especially when exporting internationally. In addition to the above iterations, there are many variants of the manufacturing processes.
Manufacturing wire and cable is complex.
The need for manufacturing accuracy
Wire and cables must be manufactured to specified parameters, e.g., dimensions, weight, conductivity, length and optical performance. These parameters must be attained within a defined cost to achieve the target margins.
Furthermore, the products must be supplied to customers on time and in full — be it from stock or made-to-order — once a plan has been agreed upon and within the constraints of overall investment in working capital. This includes raw materials, semi-finished products and finished products.
These highly complex processes and procedures, in turn, create many opportunities for error, waste, inefficiency and delay. As a result, manufacturing managers, supervisors, and the managers and technical specialists of the supporting functions (maintenance, process engineering, design engineering, planning, procurement, quality and technical) are often engaged in multi-disciplinary groups to solve such problems. These efforts ensure that business goals are achieved and that manufacturing can work within the required parameters daily, weekly or monthly.
Multiple data points are required to be measured and reported, and variances must be quantified and highlighted promptly. Action needs to be taken to either correct production to avoid a variance or, if one has occurred, to enable the necessary action — quarantine, concession, rework, scrap, remake, etc.
Combatting the Issues Created by the Complex Nature of Wire and Cable Manufacturing
Setting and using design standards in the business
Cable designs are produced per national and international standards and can account for any specific requirements of customers. These designs, and the tolerances that form an integral part of the designs, provide the physical parameters that manufacturing facilities must meet.
The designs also automatically determine material requirements, which in turn help generate costings, including the direct costs of processing the materials and the overheads. As a result, accurate quotations can be quickly generated for customers.
In addition, allowances for waste are factored in. These may be arbitrary or based on historical performance, whereas cost standards are usually based on historical performance and manning patterns.
Cable designers use design sheets to record the physical design parameters. How these parameters are then used within the business depends on the systems and processes in operation.
A paper-based approach
A purely paper-based approach to communications is still common practice in many wire and cable manufacturing plants.
Job cards may include an array of printed documents, including:
- Specific cable designs and associated parameters
- Weights per unit of length
- Product/cable drawing
- Expected processing times
A digital, central database approach
At the other end of the spectrum, data is entered into a digitalized, central database that is then widely used throughout the business as a single source of information.
The paper-based and digital approaches enable other systems in the business, such as manufacturing execution systems and machine control systems, to pull down data when required. This process is done automatically through software programs, where computer systems access the central database or via the manual keying-in of data by operators if using a paper-based approach.
One benefit of a centralized digital database is that it can also contain real-time information on parameters such as process times, materials consumed and waste. The alternative — and a much riskier and error-prone scenario — is when calculations are completed and then entered manually by operators.
Managing quality and cost
Managing quality and cost involves comparing actual production values with internal standards. Quality checks are typically carried out at each stage of manufacture, although measurement methods may limit their frequency. Operators may record quality and productivity data on job cards from manual, offline checks or from observations of the readouts from in-line devices.
If the physical parameters are within the tolerances of the design, then the sub-component can be passed to the next operation. It is also possible that quality control may check parameters by sampling.
Many machines used for wire and cable manufacture have in-line gauges, diameter, eccentricity, spark detectors and alarms installed. Data loggers may record data, or the gauges may provide a statistical summary. It is also possible for these devices to post data to the central database. In addition, productivity data may be recorded and the subject of review periodically.
Comparing actual quality and productivity data against a set of standards is often a manual and offline activity. It may involve sign-off by supervision or be self-approved by operators. If recorded data indicates noncompliance, then escalation may occur. Drums may be quarantined and labeled and await sentencing.
Variances in productivity issues may be reported and acted upon depending on the sophistication and focus of the production management function. For example, if data is being managed in a central database, checks can be carried out automatically.
A product can be approved for onward use at the next stage in operation or held if there is an issue. For example, if barcode scanning of inter-process drums is in place, a non-compliant, semi-finished product can be blocked from further use. Productivity data can be analyzed, and key performance indicators (KPIs) presented to production staff, e.g., overall equipment effectiveness (OEE).
Continuous improvement and problem-solving
Plan, do, study, act (PDSA)
The PDSA process is a well-established management tool in most management and supervisory courses.
The Deming Institute defines that the “PDSA Cycle (plan-do-study-act) is a systematic process for gaining valuable learning and knowledge for the continual improvement of a product, process or service.”
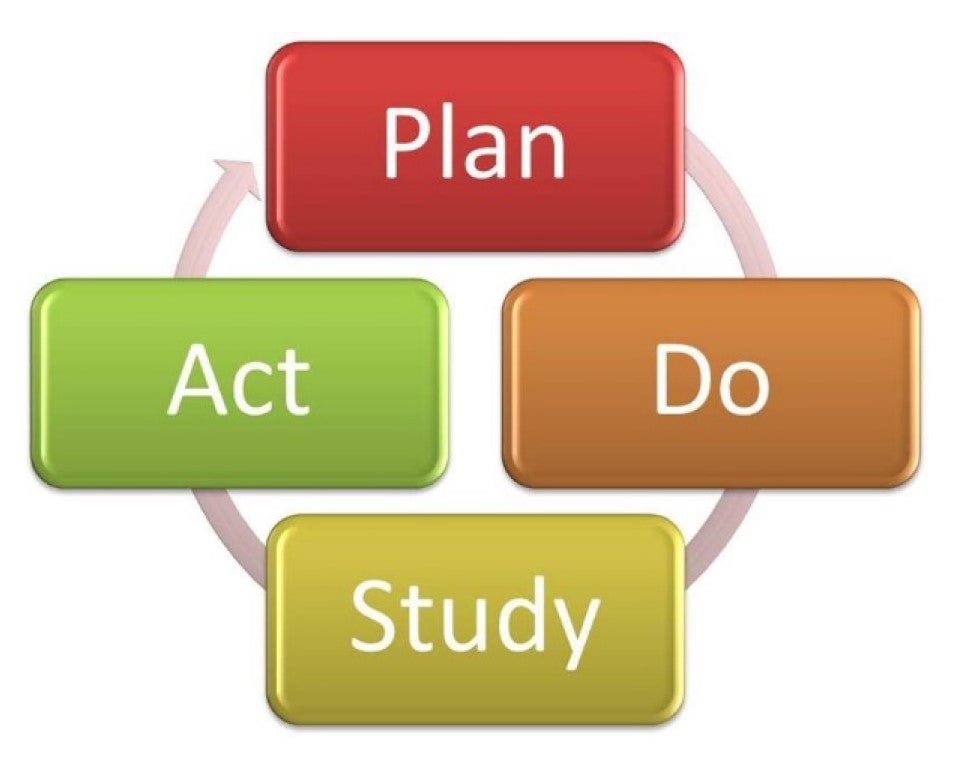
Its systematic application in cable factories is, however, often lacking in the following ways:
- Plans can be infrequent or poor.
- Studying (checking) can be ad-hoc.
- Action (or rather, corrective action) is often lacking or is more firefighting than controlled change.
- Cable factories are rarely short of people doing.
In factories where data is communicated manually, operators’ checks are the only ones taking place. It is still possible to run an effective PDSA process. It does, however, require extra diligence from supervision and management.
On the other hand, in factories that use more sophisticated, digitalized methods for communicating and managing data, the systems can do more of the PDS elements of the process. However, it still requires operators, supervisors and managers to act.
Five whys and one how (5W1H)
Another well-known problem-solving tool between study and act is the “five whys and one how” method. Asking "Why?” five times is a method for revealing the root cause of the issue, and “How” is the agreed fix. The more data and facts available to support the investigation, the more likely it will find the problem.
Operators are an invaluable source of information, but when a database of recorded information supplements their observations, the outcome can be so much more informed.
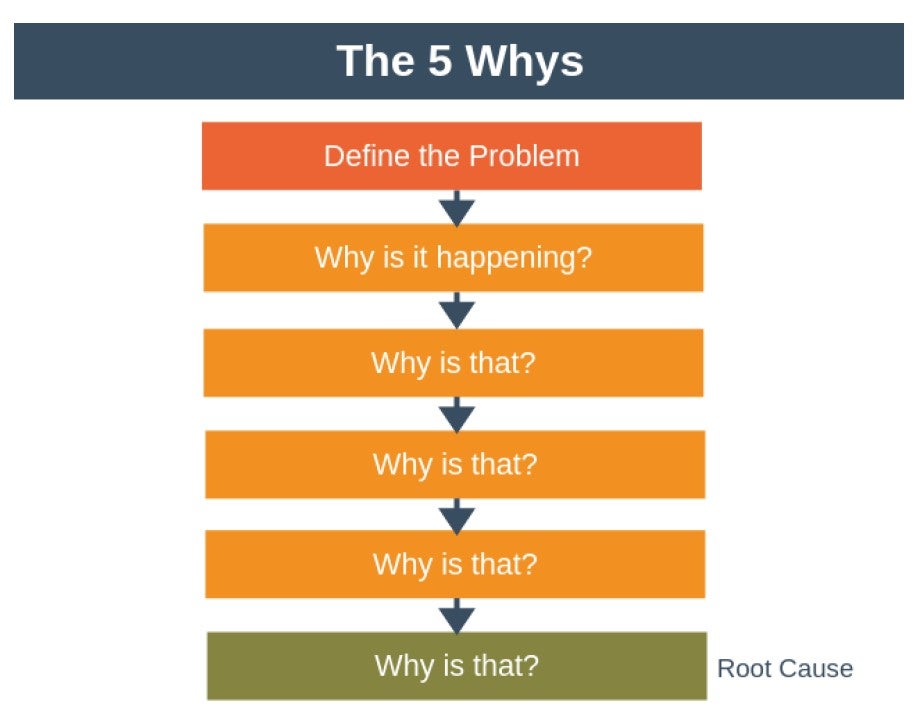
Cascade objectives, key performance indicators and management reviews
A top-down process of setting and cascading objectives is a prerequisite for any manufacturing business looking to target performance and make improvements. Senior managers should set goals annually and align them with the business strategy and budget. KPIs for the business should be defined and targets set.
These business targets should be cascaded down in a structured manner, usually at least three levels, e.g., business, manufacturing and cell/machine. The lower levels set KPIs that are aligned with the business level ones.
The measurement framework and targets should be reviewed and approved before rollout. This process provides a framework that ensures everyone in a business aims to achieve goals aligned with the business need. It also enables a drill-down so that when there is a performance variance at the top level, an analysis of the lower-level KPIs clearly indicates the source.
Application of problem-solving techniques such as “five whys and one how” can be used to review data and information to ensure root causes are identified and targeted actions developed to correct them.
Regular management reviews of performance data should be systematic, action-focused and followed up. For example, formal reviews with the leaders of each shift should be carried out daily, as should an overall review of manufacturing performance in the previous 24 hours. Such review meetings typically lead to short-term corrective actions as well as the escalation of more complex issues.
Each week information on trends and performance against targets should be reviewed alongside the setting of corrective actions and a review of escalated issues. It is usual for all business function heads to meet weekly to review the previous week’s work and assess the current week’s plan. Such meetings develop a good understanding of the functions of the impact of poor and good performance on the whole business.
Monthly meetings typically occur amongst senior managers and should be the forum to review progress towards the annual targets.
Total employee (operator) involvement
In any control system, the quicker the actuator (a device that produces a motion by converting energy and signals going into the system) adjusts a setting to maintain the desired performance, the more controlled the system is. In any manufacturing environment, the operator of a process that converts materials from one form to another is often a key element in the actuation of a change.
In cable-making, many automatic control systems are on the lines to maintain quality within defined limits — but not for all parameters. Providing an operator with all the information they may need, in real time, to avoid an error or to make corrections before a non-conformance occurs is good practice.
So, providing all relevant design targets and process settings is a prerequisite, and giving live feedback on performance against them is essential. Operators must be empowered, within limits, to make the required adjustments.
Often a supervisor’s intervention may also be required. To do this, supervisors must be quickly alerted to developing issues and warnings of any impending problems to be truly effective.
Modern management of wire and cable manufacturing
Given the complex nature of cable manufacture, the multitude of potential problems that can arise, and the need for effective and timely feedback on performance to facilitate corrective action, it requires efficient and continuous two-way, or even multi-way, communication.
This can be achieved by paper-based instructions and data recording coupled with visual control techniques; however, this method is time-consuming, labor-intensive and prone to error. Digital processes and devices most effectively provide the necessary communication, data recording and reporting.
The benefits of implementing digital processes and devices
- A speed-up of communication between processes
- Facilitates filtering of fundamental issues
- A speed-up of the escalation of a problem
- Fast reporting and control of performance on a wide range of indicators
- The ability to manufacture using a more comprehensive range of indicators (in real time) than is humanly possible
Digital tools undoubtedly support attaining and maintaining World Class Manufacturing performance status when used as part of a well-tuned management process, which begins with empowered operators directed by well-informed, action-oriented managers and supervisors.
Providing operators, supervisors and manufacturing managers with timely performance information, be it delivery to schedule, material waste, productivity or quality, is at the forefront of an objective-led culture populated with informed and motivated staff.
Digital solutions
Cable design solutions
The design, costing and quotation software, CableBuilder Enterprise, is now used in hundreds of factories worldwide to simplify the complex management of cable-design data, from the initial design concept to delivering the full bill-of-materials directly to the ERP system.
Strengthening the CableBuilder offering, CableBuilder Go was launched specifically for single-factory and smaller manufacturers. This innovative software drives improvements such as faster design and quotations and more accurate costing.
Manufacturing execution system (MES) for wire and cable
CableMES further aims to support wire and cable manufacturers to effectively plan, manage and control the manufacturing process. CableMES uses the latest Industrial Internet of Things (IIoT) technology to optimize large-scale cable manufacturing operations.
Demonstrations of all products and consultations are available.
Conclusions
There is a saying: “No one likes to do a bad job,” and providing manufacturing staff with all relevant information can empower them to do an excellent job.
An investment in a digital approach must be part of a business’s manufacturing strategy and an integral part of its IT strategy.
Procurement decisions on manufacturing plants, equipment, and measurement devices must also be aligned.
Too many businesses split these decisions across different functional areas due to lacking an integrated strategy. Islands of automation result from manual data entry, recording, and analysis. This ultimately limits the effectiveness and competitiveness of the business.
Key takeaways
Wire and cable manufacturing is complex and error-prone
The many different processes, machines, standards and countless product iterations make wire and cable manufacturing complex. Furthermore, the need to work within specified parameters means these highly complex processes and procedures create many opportunities for error, waste, inefficiency and delay.
Steps to overcome daily obstacles
Complexities require manufacturing managers, supervisors, and technical specialists to engage in multi-disciplinary groups. Implementing sophisticated digitalized methods for communicating and managing data allow for gaining valuable learning and knowledge required for a product's continual improvement and production processes.
A digital approach and solution are available for wire and cable manufacturers
Effective and timely feedback on performance to facilitate corrective actions requires slick and continuous two-way or multi-way communication, most effectively provided by digital analysis and communication.
Sophisticated cable design software, cable-specific MES, and integration with enterprise resource planning (ERP) systems ensure the seamless, cost-effective, and accurate production of a product from initial customer query, design and quotation through all production processes to delivery of the end product.
Get connected with our sales team
Thanks for your interest in our products and services. Let's collect some information so we can connect you with the right person.