December 31, 2020
Hydrocarbon based refrigerants have favorable environmental characteristics, however, they introduce an added fire risk as compared to previous generations of refrigerants (Figure 1). The added fire risk is directly related to the higher flammability of hydrocarbons, especially if there is a leak in a refrigeration system. The leaked gas could be ignited by nearby hot surfaces or electrical components. To understand and address the risks, international safety standards such as EN 378, IEC 60335-2-40, IEC-60335-2-89, ISO 5149 or regional standards like ASHRAE 15 or UL 60335-2-40 (for the U.S.) prescribe physical test methods. However, there is a challenge and a limit to using physical testing to thoroughly understand the potential risks associated with leakage of a combustible refrigerant in confined spaces.
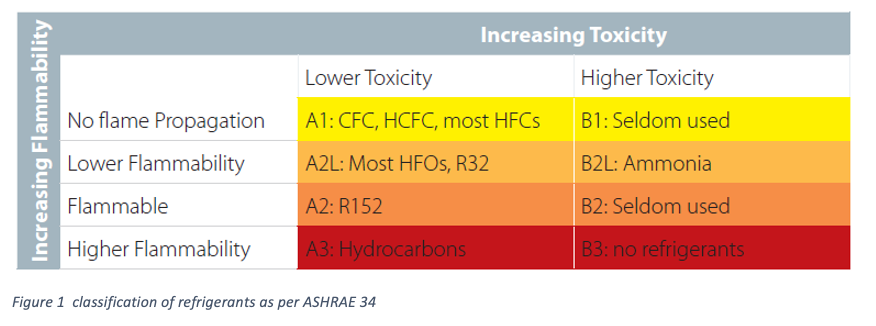
A central challenge is that physical testing, especially if it could involve fire and explosion, can be labor intensive and costly. Given that many tests must be conducted to produce the necessary insights on the potential risks, this can become a very expensive endeavor. Yet, there is another limit of physical testing that is more problematic. It is only possible to capture data at discrete points in a physical test setup. These discrete points are usually selected to address the specific question the test was designed to answer and so the data collected may not provide sufficient insight into the testing conditions or allow for generalization. And if this were not enough, there is another challenge for refrigeration systems that operate at very high charge levels. The physical testing of such systems for safety can itself require substantial infrastructure that is not commonly available.
A valuable and insightful complement to physical testing is the use of computational modeling tools. Computational modeling tools come in many different flavors from finite element based to meshless methods that help predict the physical phenomenon in many different disciplines from mechanical to thermal/fluid to electromagnetics. Over the years, these tools have been used to help understand the risks associated with leakage of combustible refrigerants [1]. For modeling, the key challenge is to validate the simulation, that is, to demonstrate via experimental evidence and rigorous modeling process review, that the model predictions are accurate.
To demonstrate the potential of simulation and to quantify its accuracy, UL built a computational fluid dynamics (CFD) model intended to replicate results seen during refrigerant leakage testing conducted for an AHRI funded project [2]. Since the concern is with flammability, it is only necessary to know the concentration levels of the leaked refrigerant gas throughout a space and compare it to the lower and upper flammability limits of the refrigerant. If the concentration levels reside within the limits, then there is a chance of fire in the presence of an ignition source. Using CFD analysis, UL built a model of the testing room and recreated the same leakage scenarios as those conducted in the physical tests. In each scenario, the refrigerant concentrations were calculated at specific sensor locations available from the test, over the time frame of the test. Results for one scenario and one sensor location are shown in Figure 2.
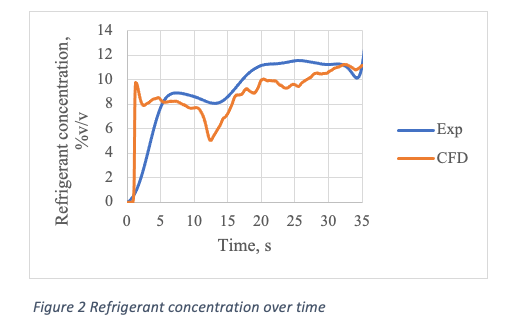
The true power of modeling is that the results can go beyond simply looking at the concentration levels within one location or even a handful of locations. The model provides results throughout a tested space. One example of a visualization of the concentration in a room for one scenario at a point in time is shown in Figure 3.
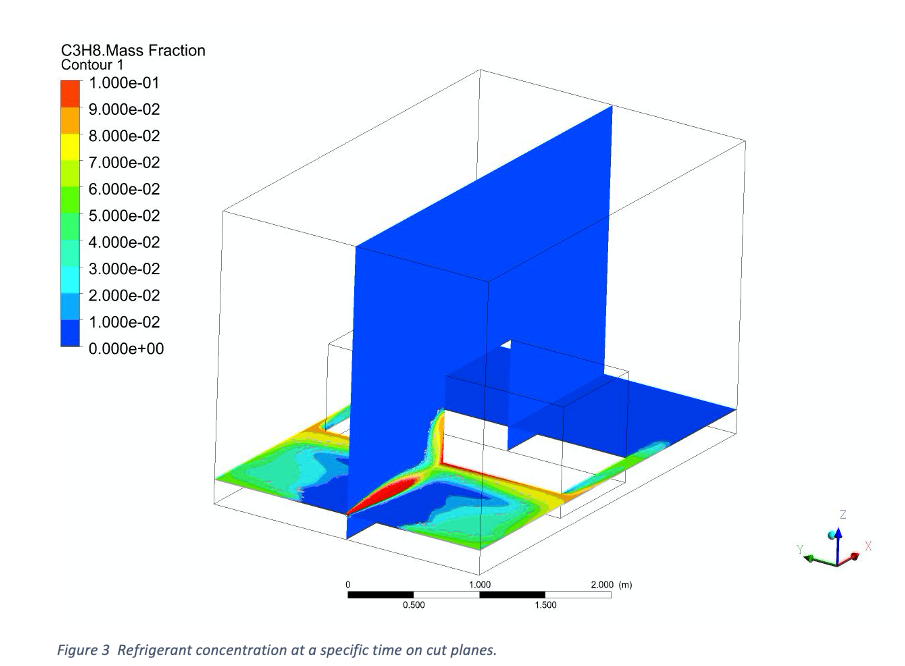
Now, we took this analysis one step further. Since we know the concentration levels throughout the room, we focused on tracking the volume of the leaked refrigerant gas that contains concentration levels between the upper and lower flammability limits. This is what we call the flammability volume (FV). With such a volume being tracked, we created the Normalized Flammability Volume (NFV) as a parameter to track fire safety risk for leaked refrigerants. The FV is normalized by a portion of the volume of the entire room, called the volume of interest (VOI), where the ignition sources are most likely to reside. The values of NFV will reside between 0 and 1 with a higher value suggestive of a higher risk of fire or explosion [3]. So more generally, the equation is as follows.
NFV = FV (in VOI)/ VOI
The flammable volume can be quantified over any time frame using data generated by a high confidence CFD model (Figure 4). The use of modeling and simulation coupled with targeted physical tests can provide the insights needed to help ensure safety in equipment design [4].
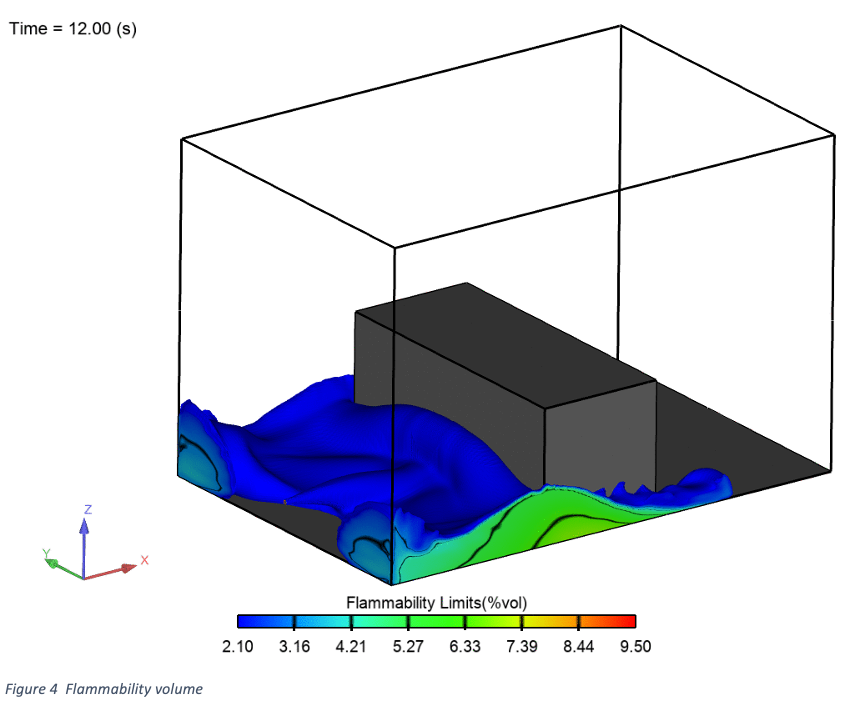
The value of modeling and simulation depends greatly on the establishing the accuracy and applicability of the predictions. As the use of modeling and simulation grows, it is important that a proper framework is available to assess the accuracy and applicability of model predictions especially when applied to certification decisions. UL offers a Model Verification & Validation (MV&V) assessment that helps manufacturers incorporate the predictions from a model to support a certification or safety risk activity. The MV&V assessment is built on standards and best practices gathered from a variety of industry groups and professional associations such as American Society of Mechanical Engineers (ASME), International Association for the Engineering Modeling, Analysis and Simulation Community (NAFEMS) and National Aeronautics and Space Agency (NASA). Simply stated, the purpose of Verification is to establish that used equations are being solved correctly. Validation is about establishing that the equations being solved are relevant and representative of the problem at hand.
As for the specific area of refrigerant fire safety due to gaseous phase leakage, we have shown that modeling and simulation can provide accurate predictions when built correctly. This is a critical point. It may be possible that models built by two different groups could seemingly show the same accuracy. However, upon closer examination, it might be found that one group used inputs that were tuned to help the model match the test results. That is why UL offers this unique MV&V service by gathering evidence and technically evaluating a range of factors for any model submission: mesh refinement, comparison of test and model results at many different points within the test domain, a description and justification of the underlying physics, traceability on the material properties as independent inputs, along with other factors.
Physical testing is still important but its value is less in how it generates insights directly to understand a risk. Instead its value is more and more in how it helps advance the use of computer-based engineering modeling and simulation tools.
[1] S. Hosur, S. K. Rai, M. Tabaddor, “Refrigerant Gas Leakage in ISO Room: A Comparative CFD Study” Advances in Engineering Design and Simulation, Lecture Notes on Multidisciplinary Industrial Engineering, https://doi.org/10.1007/978-981-13-8468-4_1
[2] Underwriters Laboratories Research Report, March 2019, AHRTI Report No. 9007-02, Benchmarking Risk by Whole Room Scale Leaks and Ignitions Testing of A3 Refrigerants.
[3] S. Hosur, M. Tabaddor “A NOVEL SIMULATION-BASED FIRE RISK HAZARD RANKING FOR REFRIGERANT LEAKAGE IN CONFINED SPACES” research report 2018, UL Inc.
[4] Flammable Refrigerant modeling for Equipment design and certification, On-Demand Webinar, UL, 2020, https://www.ul.com/resources/flammable-refrigerant-modeling-equipment-design-and-certification
Get connected with our sales team
Thanks for your interest in our products and services. Let's collect some information so we can connect you with the right person.